Accessories for pressure reactors
Our vast range of accessories helps you to adapt your reactor systems to continuously changing process requirements and operational procedures.
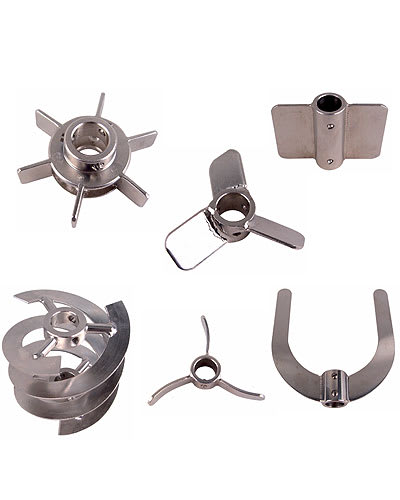
Agitators, stirrers
Depending on the stirring or mixing task, Buchi reactors can be equipped with stirrers of different types.
For gas entrainment as in hydrogenations, the Rushton type turbine stirrer is often used.
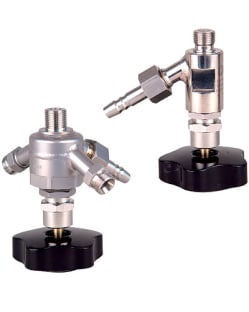
Bottom outlet valves
Inner diameter: DN3 - DN25
Temperature: 350 °C
Pressure: 350 / 500 bar - 5000 / 7000 psi
Material: stainless steel, Hastelloy®, Titanium etc.
Buchi bottom valves are very compact, available for different operating conditions and functions. Solenoid bottom valves with a pneumatic actuator are used for automated opening / closing with signal feedback of the status.
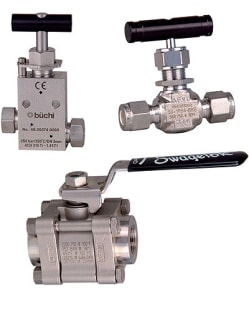
Needle valves, ball valves
Needle valves and ball valves for low and high pressures are installed on the reactor head as needed. Solenoid needle and ball valves with pneumatic actuators are used for automated opening / closing with signal feedback of the status.
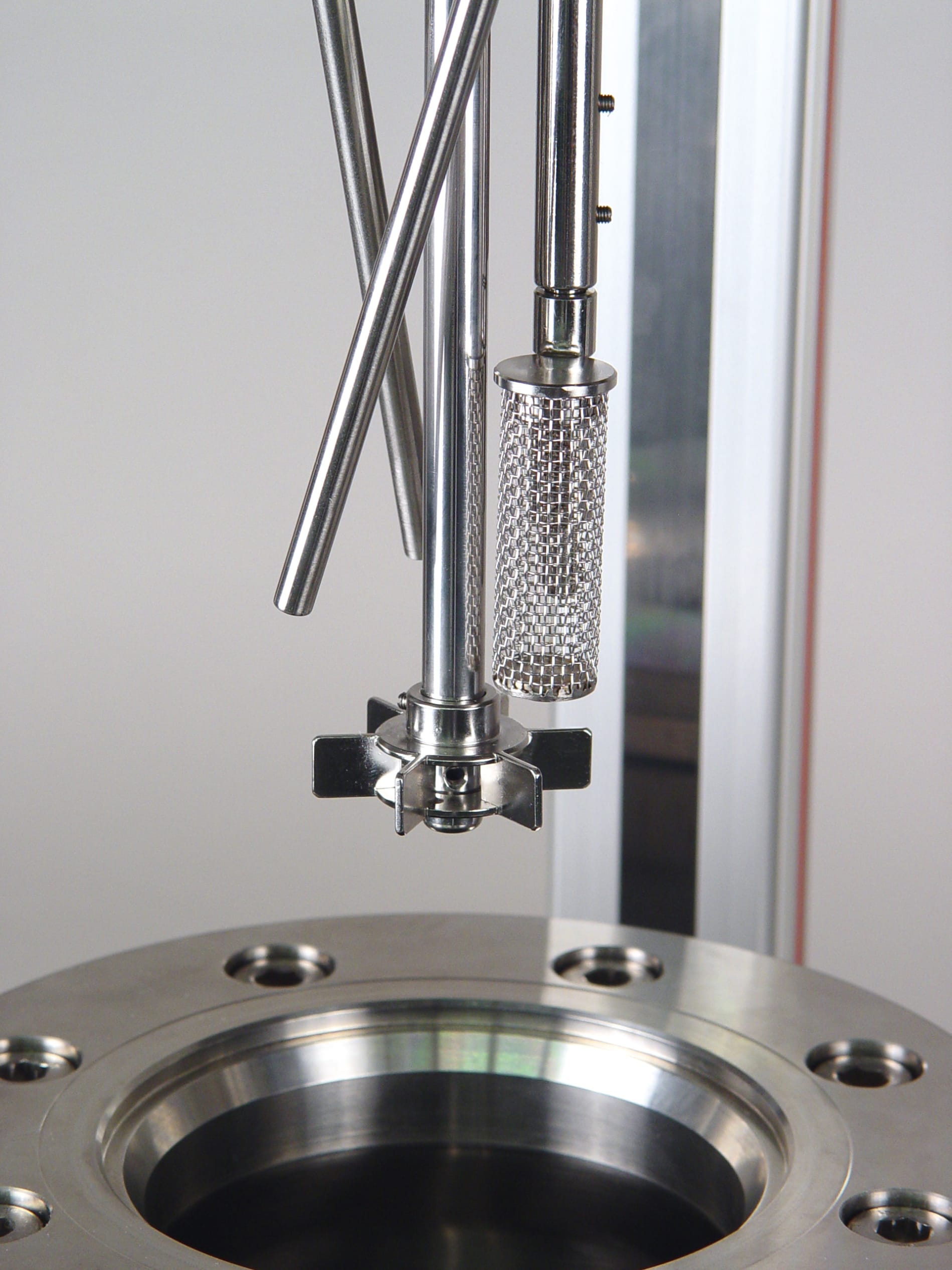
Catalyst testing, catalyst screening
Catalyst testing covers several types of research such as catalyst effectiveness, yield, activation, lifetime and regeneration.
The type of catalyst baskets varies depending on the catalyst being used, the interaction with the chemistry, the temperature, the pressure and the number of catalysts in the basket. Exposure to the reactants can be done through a stationary catalyst bed or a spinning basket.
Our special accessories offer solutions for more complex problems in pressure reactions in the field of catalyst research.
Examples
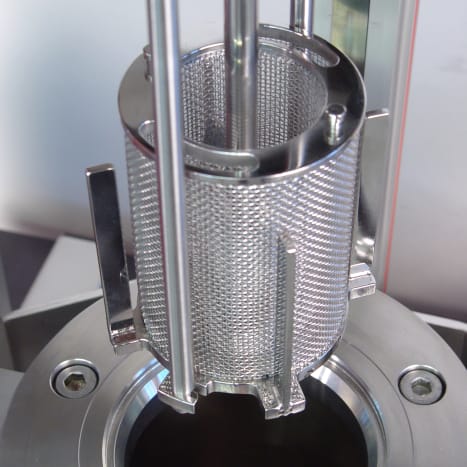
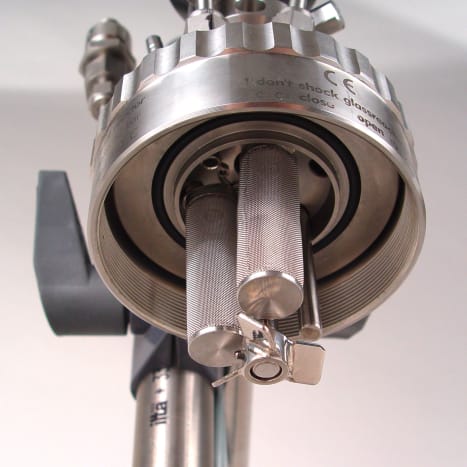
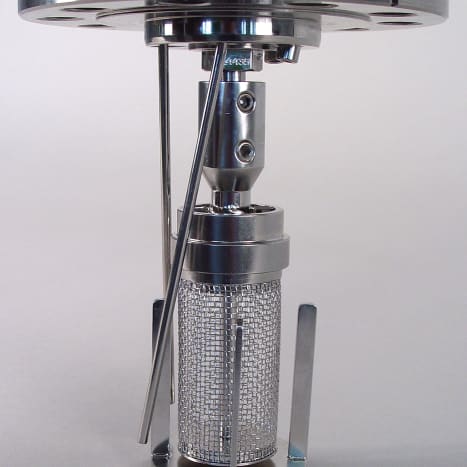
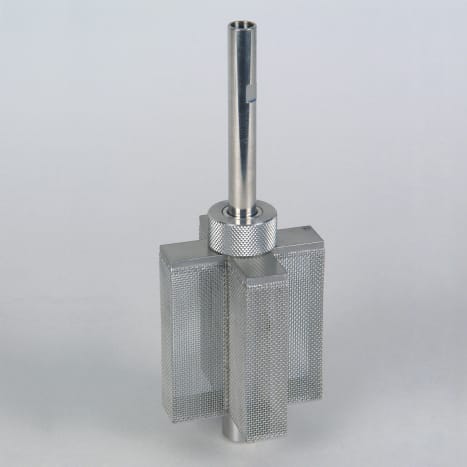
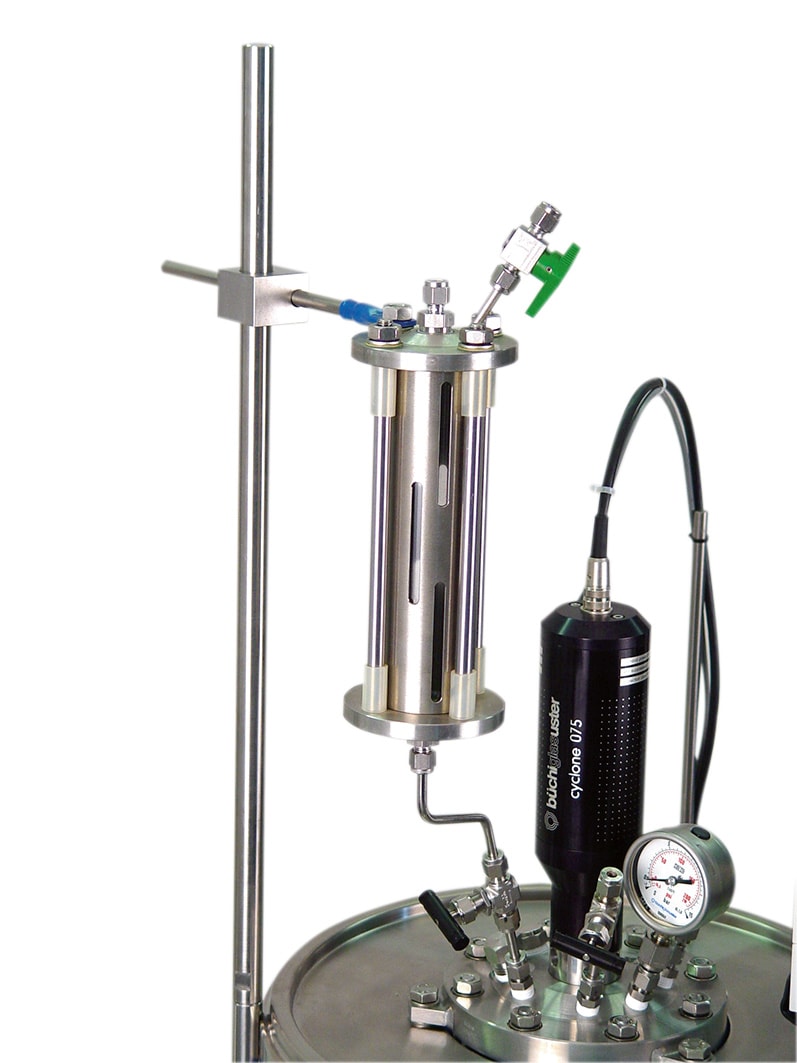
Feeding of liquids, solid, gas
Burettes
Volume: 10 - 1000 ml
Pressure: depending on material
Material: Glass, stainless steel, Hastelloy®
Burettes are available in glass with protective jacket or as full metal version for higher pressures with sightglass. Feeding funnels enable fast charge of solids and liquids.
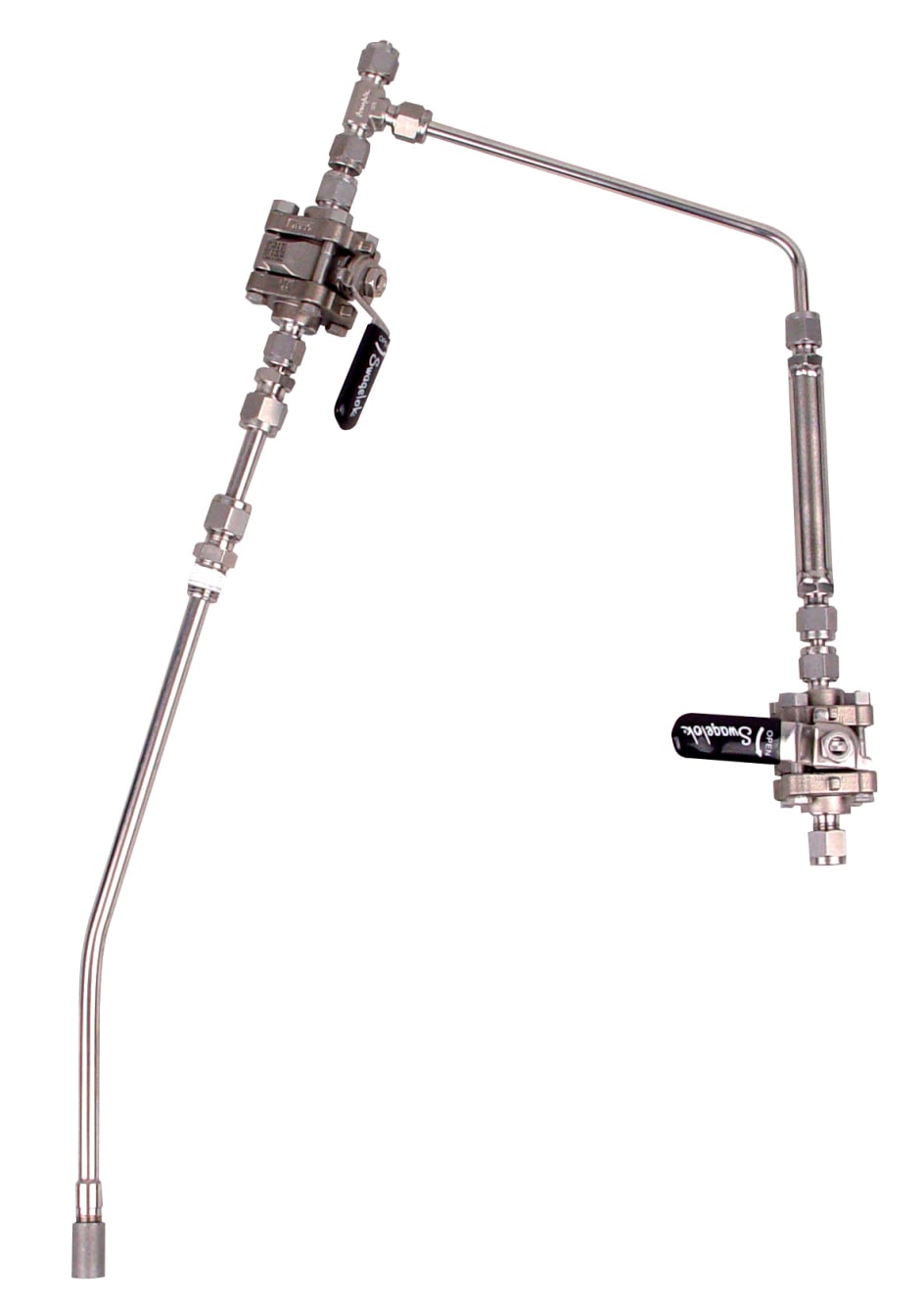
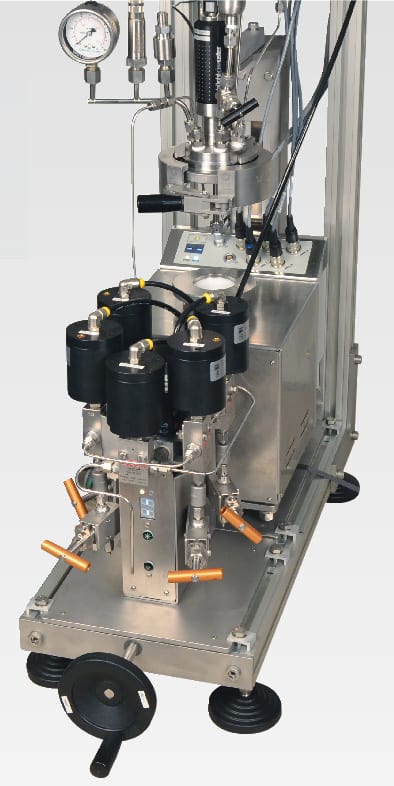
Sampling systems for manual and automated sampling
Systems for manual and automated sampling (up to 4 samples per run) during pressure reactions, see also Parallel Pressure Reactor system PPR.
Sampling system for pressure reactors,
Sampling with the reactor under pressure,
with immersion tube and filter, sampling cylinder,
Connection for flushing the lines and sampling cylinder
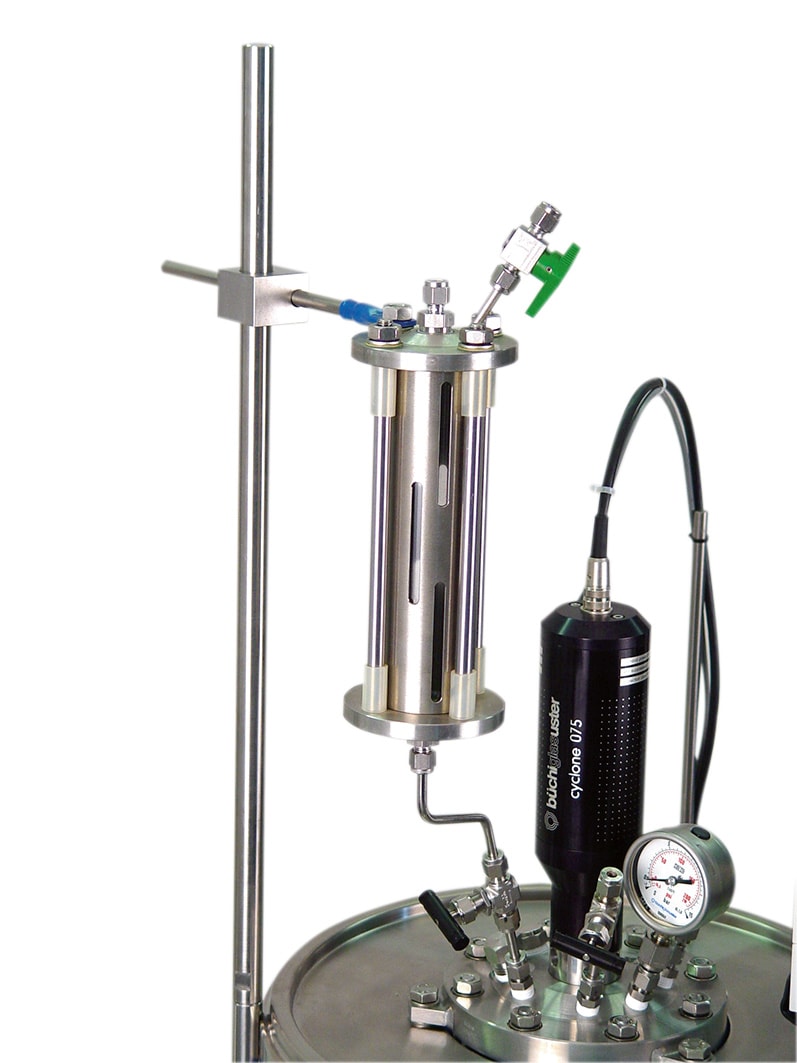
Burettes, feeding funnel
Burettes
Volume: 10 - 1000 ml
Pressure: depending on material
Material: Glass, stainless steel, Hastelloy®
Burettes are available in glass with protective jacket or as full metal version for higher pressures with sightglass. Feeding funnels enable fast charge of solids and liquids.
Examples
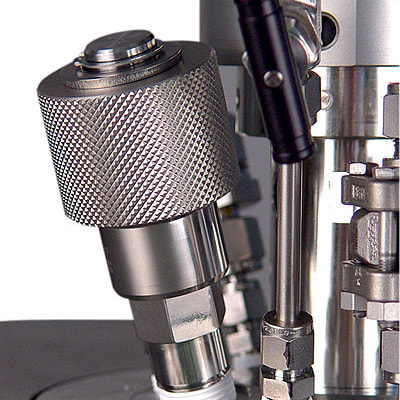
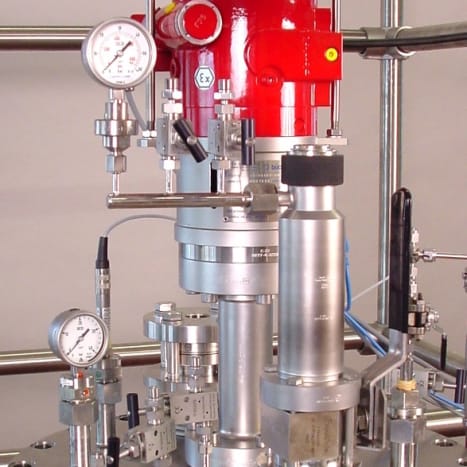
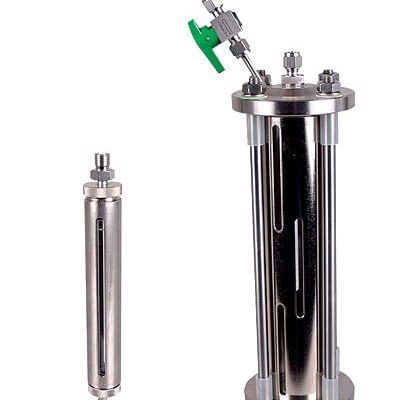
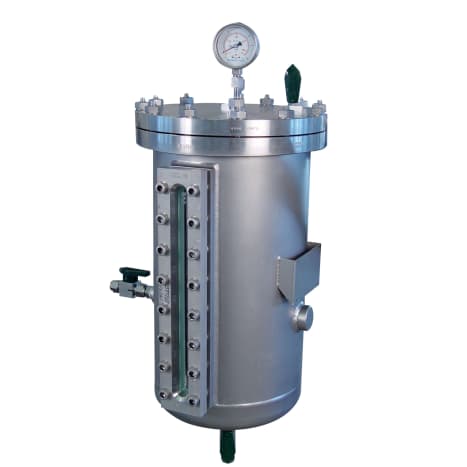
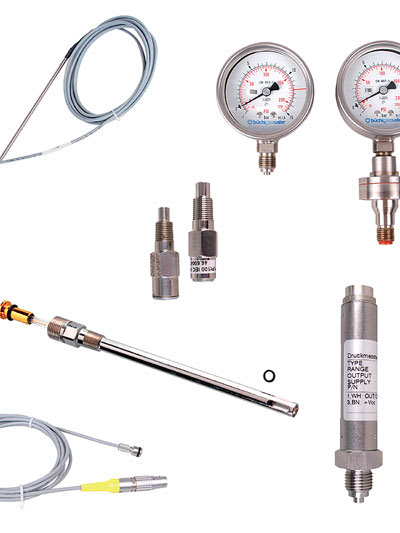
Probes for process control
Probes are available to measure the different process parameters. These values can be displayed on our monitoring instrument and recorded in our bls software.
Frequently measured parameters are:
- temperature
- pressure
- stirrer speed
- torque
- pH
IR probes, probes to control particle sizes etc. from other suppliers can be integrated into our pressure reactors or stirred autoclaves.
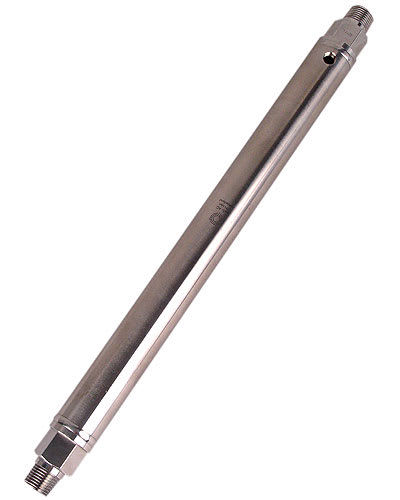
Complete setups for reflux distillation under vacuum and pressure
In chemical processing, especially when working with pressure reactors, efficient temperature control is crucial. Condensers and heat exchangers play a vital role in maintaining the desired thermal conditions, ensuring that reactions proceed safely and efficiently.
Reflux condensers
Reflux condensers are designed to cool and condense vapors back into liquid during distillation or other thermal processes. In pressure reactors, they are particularly important for maintaining a stable reaction environment. By allowing the condensed liquid to return to the reactor, reflux condensers help to control the reaction temperature and concentration, which is essential for both reaction efficiency and safety. These condensers are available in various materials, including glass and metal, to suit different chemical compatibility needs.
Heat exchangers for pressure reactors
Heat exchangers are essential when precise thermal management is required. Whether heating or cooling, these devices ensure that the reactor contents reach and maintain the desired temperature rapidly and uniformly. In setups where very fast temperature changes are necessary, internal heat exchangers can be integrated directly into the reactor. This allows for immediate and efficient heat transfer, making them ideal for processes that demand tight thermal control.
Complete reflux distillation setups
For applications involving distillation under vacuum or pressure, we offer complete setups that integrate seamlessly with your reactor. These systems include everything needed for efficient distillation, from columns and reflux condensers to receivers. Whether you require a glass setup for transparency and chemical resistance, or a metal system for robustness and high-pressure applications, our solutions can be tailored to your specific needs.
Customized solutions for your processes
We understand that every process is unique, which is why our condensers and heat exchangers are designed with flexibility in mind. Whether you need a simple reflux setup or a complex distillation system, we can provide customized solutions that meet your exact requirements. Our products are engineered to ensure optimal performance, safety, and longevity in demanding chemical environments.
Examples

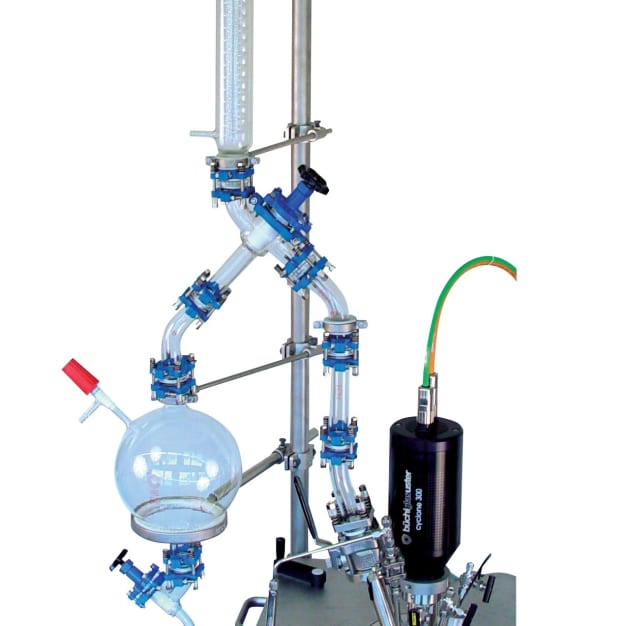
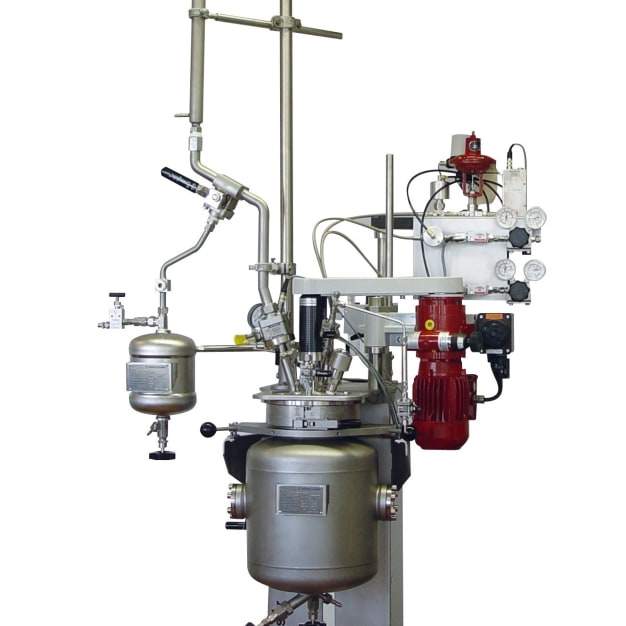
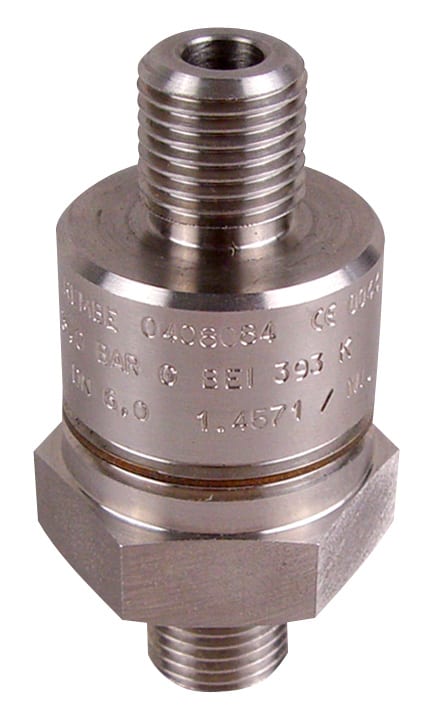
Safety devices for pressure reactors
In industries where chemical reactions occur under high pressure, safety is paramount. Pressure reactors are sophisticated pieces of equipment designed to handle such conditions, but even with the best designs, safety devices are essential to protect both personnel and equipment.
Rupture disc safety devices
Rupture discs are critical safety components in pressure reactors. They are designed to burst at a predetermined pressure, providing a rapid and controlled release of pressure to prevent catastrophic failure of the reactor. This immediate response to overpressure conditions helps to safeguard the integrity of the reactor and maintain a safe working environment.
Pressure relief valves
Pressure relief valves offer another layer of protection. Unlike rupture discs, these valves can automatically open and close to regulate pressure within the reactor, ensuring that it stays within safe limits. When the pressure exceeds a certain threshold, the valve opens to release excess pressure and then reseals to maintain the reactor’s operational pressure.
Integrated safety systems
For maximum safety, rupture discs and pressure relief valves are often used in conjunction with a blow down tank. This system safely contains and neutralizes any released gases or liquids, preventing hazardous materials from escaping into the environment. Such integrated safety systems are crucial in maintaining the safety and reliability of pressure reactors, particularly in chemical processing industries where dangerous reactions are commonplace.
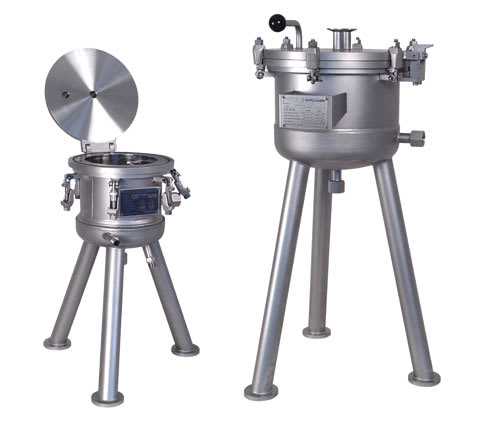
Robust and compact pressure filters
Pressure vessel: 5 to 20 liter
Pressure: -1 (FV) to 6 bar
Temperature: -10 °C to +200 °C
Material: Stainless steel, Hastelloy®, other materials upon request
Pressure filters with optional heating jacket for temperature controlled filtration. These robust and compact pressure filters are designed for filtration, pressurizing the vessel with up to 6 bar pressure.
They offer a removable filter basket, a quick opening / closing system and a perfect fit for Büchi pressure reactors, allowing easy operation.
The pressure filters are available in various sizes and filter types as well as with an optional heating jacket for temperature-controlled filtration.
Examples
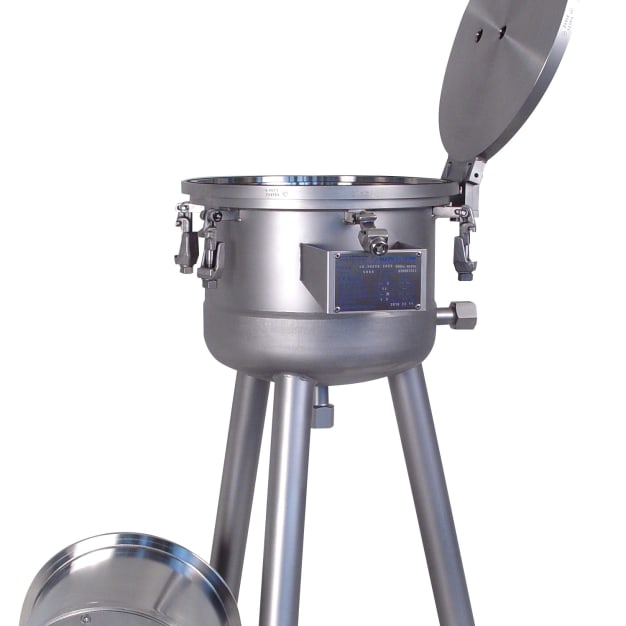
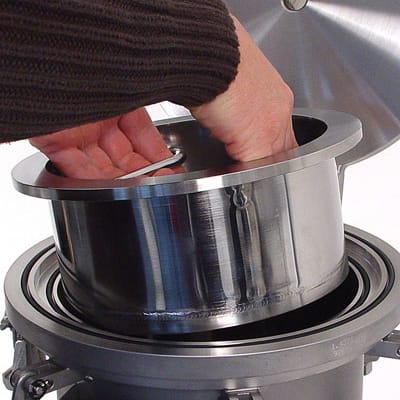
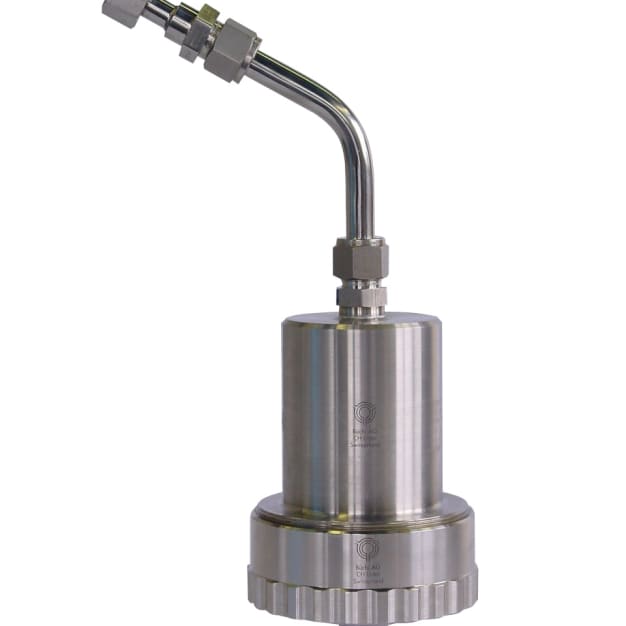
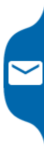